\Aluminium
die casting Moulds
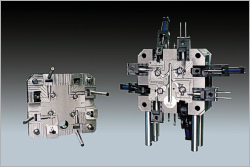
Once all the ordered materials are in the production phase begins with
the manufacture of the most important components of the moulds for aluminium
die casting: the die holder and the electrodes are built, the forging
parts are rough-machined.
These works are always done under the direction of the project manager
and in strict liaison with the production manager and the quality manager.
The quality control
dept. checks all the dimensions on a 3D measuring machine.
Once the die holder, the forging parts and the electrodes are ready the
material is sent to the supplier for the heat-treating.
Afterwards the certified hardness are checked and the forging parts are
finished through manual polishing. The mould is then assembled and closed
and its functionality is tested through a machine with the injection of
a particular resin.
Once all the parameters are tested the first sampling is done. At the
first sampling often occurs that incorrect dimensions are detected. This
could require some modifications on the mould and a new sampling has to
be done.
When the quality of the casting is good the customer has to give his written
approval of the complete project.
Moulds for aluminium die
casting have always to be delivered together with all the documentation
regarding the project (certificates of the materials, heat-treating certification,
copy of the CD containing all the project data).
The diesinker guarantees
the routine maintenance of the tooling whereas the extraordinary servicing
has to be agreed each time.
Design of tools for die casting
More
information about our products- DOCUMENTATION
|